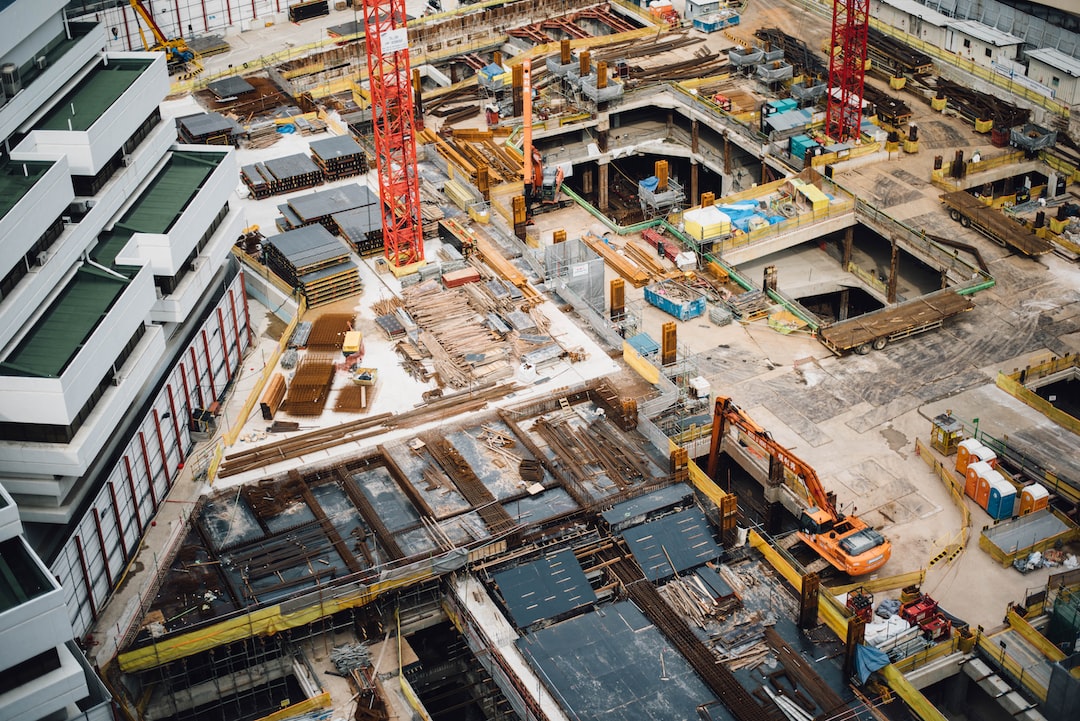
Failure Analysis: Identifying and Correcting Design Weaknesses
Share0Failure analysis is an essential process to identify the causes of failure and avoid the occurrence of such incidents in the future. In engineering design, failure analysis is an integral part of generating optimal solutions for the design of a structure or system. Identifying design weaknesses through failure analysis can save valuable resources, decrease downtime, improve safety and reliability, and optimize performance.
There are three parts of failure analysis: identification, diagnosis, and correction. The first step in identifying the underlying cause of a failure is to gather information about the conditions and events leading up to the incident. This could include data logs, physical evidence, maintenance records, and interviews with personnel involved. For example, a structural failure in a building might include inspection reports, material testing data, and blueprints.
Next, the data is analyzed, and the root cause of the failure is diagnosed. This could be a design weakness, a manufacturing defect, or an operational error. Once the cause of the failure is identified, solutions can be developed to correct the problem.
Design weaknesses can manifest in various ways, such as mechanical or functional failures or component degradation. A typical example of design weakness is increased stress on a particular component beyond its allowable limit resulting in material deformation or failure. The most problematic design weaknesses can be difficult to detect using standard design guidelines or by performing a structural analysis alone. These weaknesses can be hidden in the design itself, and only by conducting a thorough failure analysis can they be identified and corrected.
Once the cause of the failure is identified, it is essential to develop a corrective action plan. This plan should detail the necessary steps to prevent the same failure from occurring in the future. These steps may include modifying the design, improving materials, adjusting the manufacturing process, and implementing new operational protocols. After implementing the corrective action, it is important to monitor the system or structure for performance and reliability.
Design modifications following a failure analysis can improve the performance and reliability of a system. These modifications can also provide additional benefits such as reducing the weight and cost of a structure, increasing efficiency and sustainability. Correcting design weaknesses may also complement future product launches or redesigns, resulting in a competitive advantage.
In conclusion, the failure analysis process is critical in identifying and resolving weaknesses in engineering design. Identifying and correcting design weaknesses can improve the reliability, safety, and quality of products and systems while reducing downtime and material costs. Failure analysis is a continuous process and must be conducted regularly to ensure that systems and structures continue to operate safely and effectively. By conducting failure analysis, designers and engineers can learn from their failures and create stronger, more reliable products and systems.