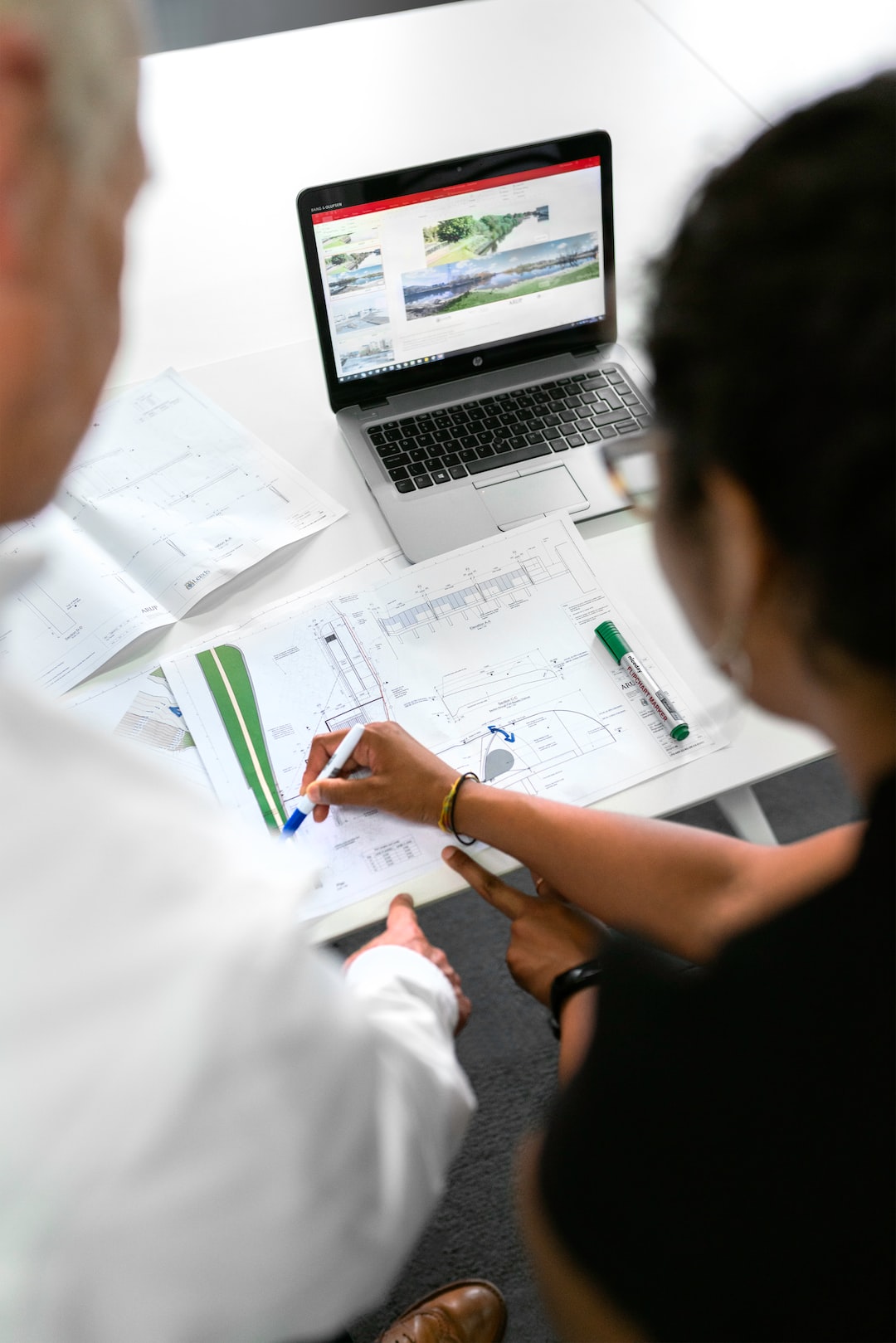
Enhancing Efficiency through Process Optimization in Industrial Engineering
Share0Enhancing Efficiency through Process Optimization in Industrial Engineering
In today’s fast-paced business environment, companies are constantly striving to become more efficient in order to increase productivity and maximize profits. One area where efficiency can be significantly improved is industrial engineering. By optimizing processes, industrial engineers can streamline operations, reduce waste, and enhance overall efficiency.
Process optimization involves analyzing and redesigning existing workflows to eliminate bottlenecks, reduce cycle times, and improve resource allocation. Industrial engineers use various tools and techniques to identify areas for improvement and implement changes that will have a positive impact on productivity and cost-effectiveness. Let’s delve deeper into the benefits and methods of process optimization in industrial engineering.
One of the main advantages of process optimization is increased productivity. By identifying and eliminating non-value-added activities, industrial engineers can significantly reduce the time it takes to complete tasks. This allows for a faster turnaround time and ultimately increases output. Additionally, by streamlining processes, industrial engineers can also reduce downtime and ensure that resources are effectively allocated to maximize productivity.
Another benefit of process optimization is cost reduction. Inefficient processes often result in wastage of resources, such as excess inventory or unnecessary labor. By analyzing workflows and identifying areas where resources are being wasted, industrial engineers can implement changes that improve resource allocation and reduce costs. For example, through the use of lean manufacturing principles, industrial engineers can eliminate unnecessary inventory and reduce material waste, resulting in significant cost savings for the organization.
Process optimization also leads to improved quality and customer satisfaction. Through the identification and elimination of process bottlenecks, industrial engineers can ensure that products are manufactured to the highest quality standards and delivered on time. By reducing cycle times and increasing efficiency, industrial engineering plays a crucial role in meeting customer expectations and enhancing overall satisfaction.
To achieve process optimization, industrial engineers employ various tools and techniques. One commonly used tool is value stream mapping (VSM), which involves creating a visual representation of the entire workflow, from raw materials to the finished product. Through VSM, industrial engineers can identify areas of waste and inefficiency and develop strategies to eliminate them.
Another popular technique is Six Sigma, a data-driven methodology aimed at reducing defects and variability in processes. Through the use of statistical analysis and advanced problem-solving tools, Six Sigma enables industrial engineers to identify root causes of problems and devise solutions that enhance efficiency.
Furthermore, the use of automation and robotics has revolutionized process optimization in industrial engineering. By automating repetitive and time-consuming tasks, companies can reduce reliance on manual labor and increase efficiency. Industrial engineers play a pivotal role in implementing and integrating automation technologies into existing workflows to streamline operations and optimize productivity.
In conclusion, enhancing efficiency through process optimization is a critical aspect of industrial engineering. By analyzing and redesigning workflows to eliminate waste and improve resource allocation, industrial engineers can significantly improve productivity, reduce costs, and enhance customer satisfaction. Through the use of tools and techniques such as value stream mapping, Six Sigma, and automation, industrial engineering continues to play a vital role in driving efficiency and profitability in today’s competitive business landscape.