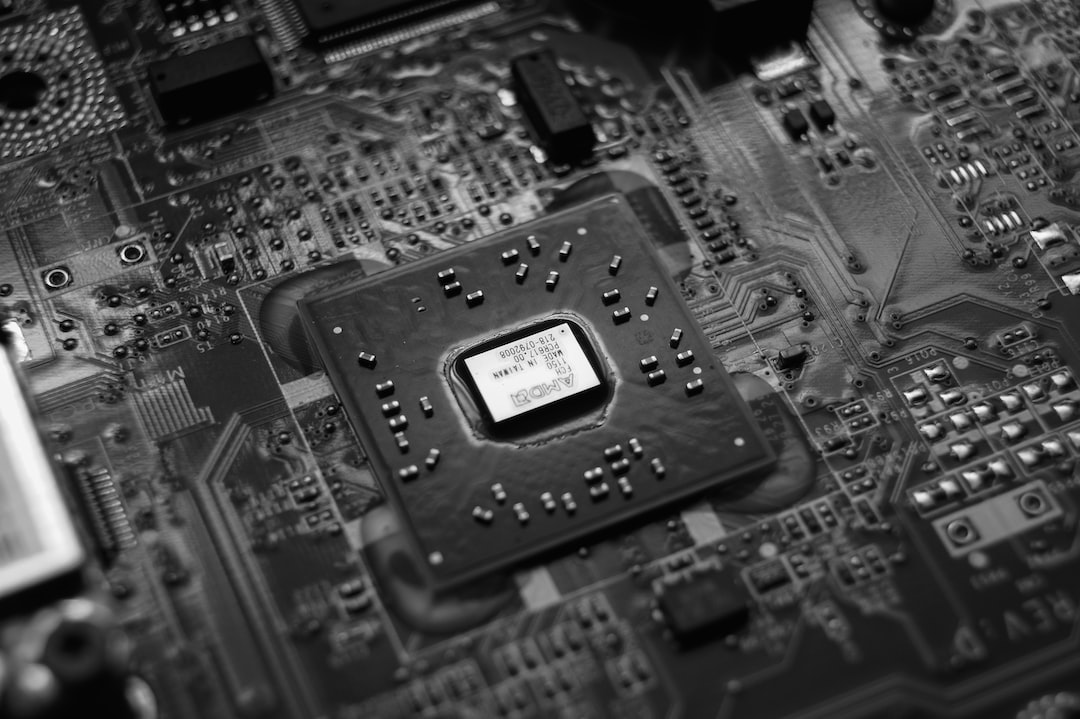
Maximizing Quality Control for High-End Production
Share0High-end production requires a level of quality control that is unmatched in other industries. The intricate details and focus on perfection make it imperative for manufacturers to utilize the best quality control practices to minimize errors and delays in production. Many factors contribute to a successful quality control process, including proper training of employees, the use of sophisticated equipment, and good communication among team members.
One of the most significant aspects of quality control is employee training. Manufacturers should seek to train employees on the specifics of their products, processes, and equipment. This will ensure that they understand the expectations, the benchmarks for success, and how to use the machinery or instruments correctly. Proper training and education of employees can provide them with the tools and knowledge necessary to identify potential issues before they become major problems, thus improving the overall production process.
In addition to training, manufacturers should invest in the highest-quality equipment and instruments available. There’s no substitute for precision equipment in high-end production. Ensuring that equipment is well-maintained, calibrated regularly, and replaced when necessary is an essential component to maximize quality control. Investing in state-of-the-art machinery, such as CNC machines, can significantly improve the accuracy and speed of production.
Good communication is essential in high-end production. Regular meetings should be held with everyone associated with the production process to ensure that everyone is aware of the goals and progress of the project. Additionally, efficient communication among team members helps to avoid misunderstandings and workflow issues, decreasing the possibility of errors.
Quality control should be a part of every stage of the production process. Manufacturers must set clear quality standards from the design stage through to the final production. This incorporates the inspection of raw materials and a final inspection of the finished goods. The selection of the proper raw material, such as metals or plastics, is also essential to ensure that the end product is of the highest quality. Raw materials should be tested and inspected carefully before use to ensure their suitability for the intended purpose.
Continuous monitoring of the production process is an essential component of maximizing quality control. Manufacturers use statistical process control to comprehend how the production process is performing. This enables manufacturers to take corrective action before significant issues occur, cutting down on manufacturing delays and improving the overall production process.
Another crucial aspect of quality control is feedback. Listening to feedback from customers, employees, and other stakeholders can help manufacturers to identify areas of the production process that require improvement. Regular feedback can enable manufacturers to establish a culture of continuous improvement, ultimately resulting in better-quality products, higher customer satisfaction, and increased market share.
In conclusion, maximizing quality control in high-end production requires a comprehensive approach that covers every stage of production. Manufacturers must invest in employee training, state-of-the-art equipment, and efficient communication to minimize errors and maximize customer satisfaction. By implementing best practices in quality control, manufacturers can develop an efficient and error-free production process, resulting in a reputation for delivering high-quality products.